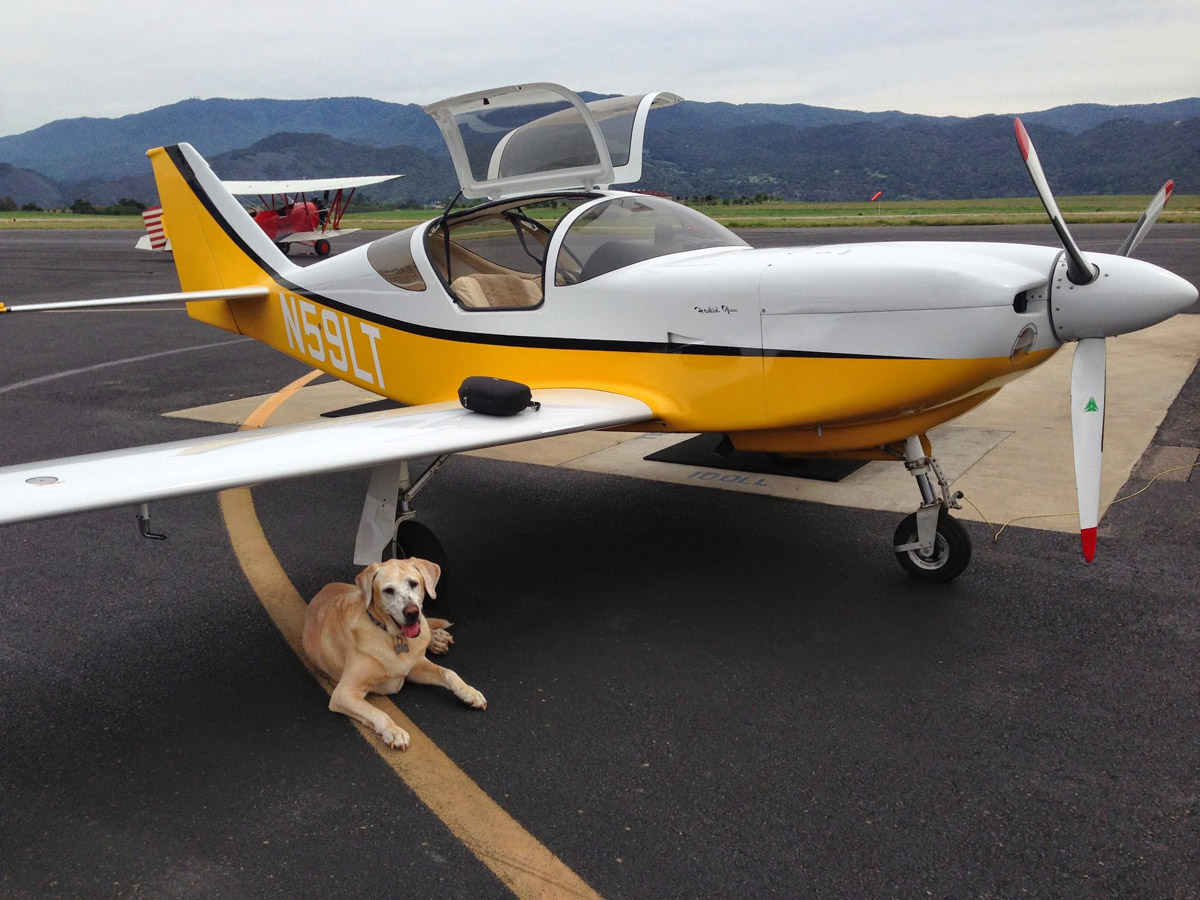
I have had more than my share of issues with the retracts on my Glasair II RG:
- Actuator Leaks
- Hydraulic pressure gauge cracked and leaking with no external drips
- Manual pump extension required on a flight
- More actuator leaks
- Relay failure on the gear control board • Manual pump extension required, again
- Pressure bleed down after gear extension
The latest was pressure failing to hold after gear extension. I returned one night from a short trip to San Jose. On dropping the gear for a landing I got three green and the pump shut off. Then I watched the pressure fall to zero pretty fast. I went around and cycled the gear. Same behavior, down and locked, and then pressure falling off rapidly.
I had to make the landing count and carefully greased it on, easy on the brakes, tracking straight as I could. During the rollout the pump cycled once or twice bumping the pressure up. So I knew that the system was generally working.

Carefully taxied to the hangar with the pump bumping the pressure up every 10 seconds or so. Deeper investigation yielded some aluminum particulates in the fluid. Very tiny and not too much. As a precaution I ordered a new pump. Oildyne Part number: 775616—about $88, I think.
I also tried to order new relief valves. They run about $210 for 2 thermal relief valves and 2 pressure relief valves. I asked f there was anything that included them that might be cheaper since $300 for the parts was almost into the same range as complete power units with a motor and reservoir.
The distributor identified an “adapter” which is the aluminum housing that was supposed to come with the relief valves for about $80—sold! After 3 weeks, the parts finally arrived, but the adapter was wrong. I was trying to work direct with Parker/Oildyne support on getting the right one, but I think they have decided to not respond to my request for help regarding buying the correct relief valves.
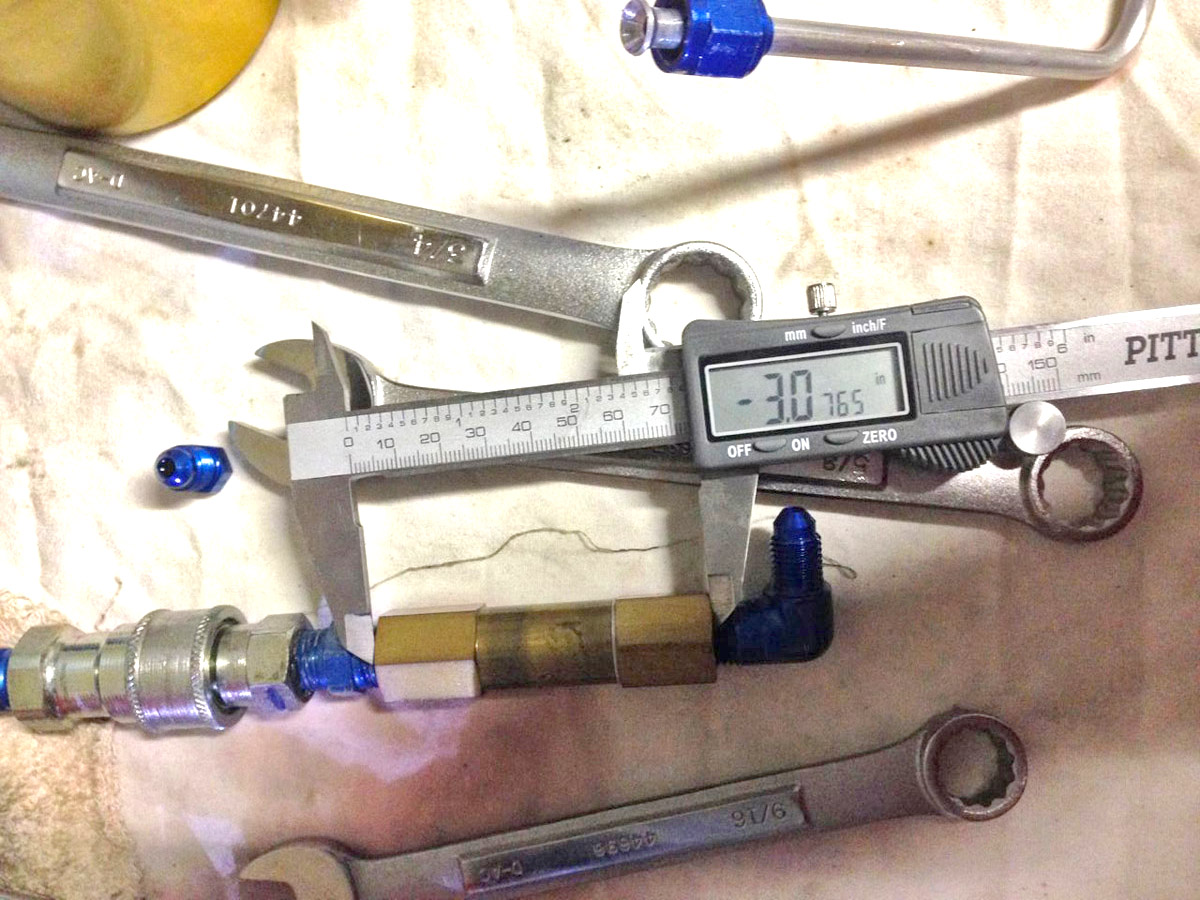
It came with the housing and the thermal relief valves ($70 each) but not the pressure relief valves and it didn’t have the hole drilled for the dipstick.
I was getting replacement relief valves just as a precaution since I was tearing everything apart. The plane only has 500 hours on it, so it didn’t seem like it should need all new parts, but considering how much effort is involved in pulling/ replacing the power unit, it seemed like a smart approach.
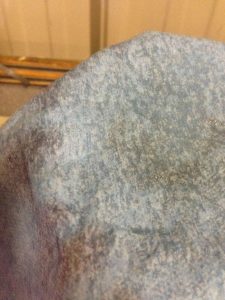
I took apart the rest of the system and the lines up to the filters. Good thing I have the filters. The pump was making a fair bit of metal and the filters had trapped it for the most part.
The filters are 60 micron NuPro with 1/4 NPT fittings. I haven’t been able to locate a replacement part number to share, but you can pretty easily find the filter inserts.
I haven’t disassembled the pump again, but I suspect I will find some particulates in the check valve or relief valve that are causing the rapid bleed down. Hopefully no damage to the check valve seats since the housing that was sent was not a direct replacement.
I can say that I am very glad to have the filters in place.
Line filters
The filters are installed about 1 foot downstream from the pump before it goes into the manifold. I learned that the system has quick release connectors above the filters to ease their removal and cleaning. So that’s a good thing to know.
When I first purchased the plane I had a request about the pump design and had contacted them and made the mistake of saying it was for an aircraft I had purchased although I never stated it was experimental.
He mentioned that they no longer sold to the experimental aircraft market. That is the same person that responded to my recent request for support which did not mention what it was for, only that I had trouble with what I had received.
They have since gone radio silent to a couple of additional emails I have sent. I’m sort of guessing I have been blacklisted at this point. Annoying.
Post-annual recap
The annual took about 80 person-hours of work. Tidied up a lot of little annoying things or things I would have done differently. Took care of a lot of maintenance items that had been neglected to one degree or another.
The gear pump was the main problem I was dealing with and waiting on parts. After Parker went radio silent on me, I decided to just clean and reinstall the pressure relief valves.
The power unit adapter that I had purchased that was not delivered to the spec I thought I ordered proved useful though. I used the poppet valves, seats, and spool out of that to rebuild my power unit adapter with all fresh parts.
Under the down pressure relief valve I found a tiny particle of aluminum that was wedged under the ball. It was flat, like placer gold and wasn’t going anywhere without some force.
After cleaning, flushing and reassembly with the new pump unit, my gear cycle time is now 50% faster. Previously it was about 15 seconds. Now it is 8 seconds. The pump that I ordered was the .327 volume pump—I suspect my old pump was a lower volume pump. There was a service bulletin about changing to the higher volume pump back in the mid-90s. I suspect that may not have been addressed on my plane.
The other issue I found was that I needed to bleed the lines to the shuttle valve for my pressure gauge. I think I had some air in there that was contributing to a little bleed down of pressure.
Unfortunately, despite assembling the pump exactly how I had disassembled it for the pressure valves. I found that the low pressure relief valve was set too high. That took me two separate remove-and-adjust cycles to get the pressure relief on the downside to about 750 psi.
I am approaching pit crew speed of hydraulic pump removal on my plane though. Hopefully something that I do not need to do for a long time now.