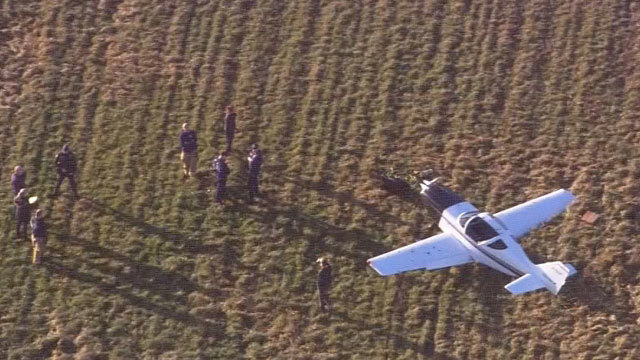
Aircraft experienced electrical failure and made forced landing off airport in Arlington, Washington
A single-engine plane landed without its gear fully extended near Arlington Municipal Airport, according to the FAA’s Pacific Division.
Advertisement
Is there some definitive procedure published for various landing gear malfunctions? There are several scenarios I have in mind:
—Hydraulic pump failure
—Loss of all electrical power
—Loss of hydraulic fluid
Or is it one procedure in the handbook that fits all situations?
This would be for a Glasair II RG
Hello Charles
I was the guy flying the Glasair IIRG in the photo sitting in-the farmer’s field. I had purchased a new lightweight Whirlwind propeller and decided that I needed to move the engine fwd six inches to correct the CG issue that resulted. This created a cascade of changes in the engine compartment which resulted in the air plane being grounded for over a year while all the changes were made to accommodate the new prop.
Anyway a long story short here’s what occurred.
Because this was the second maintenance test flight, and the first one had gone so well, that my biggest concern was to get airborne as quickly as possible to continue breaking in the engine. I had installed a brand new lithium battery for my main battery and a small aux battery, solely, to be used for my new electronic ignition.
That day I put a battery charger on the battery then I went into my new EFIS displays to reset some engine warning limits and review my engine operating parameters. I worked on the readouts for about thirty minutes. It was a cold January morning so I decided to pre heat the engine and asked my maintenance tech if he couldn’t rig up an engine heater. In about five mins he had heat going into the engine compartment while I was waiting for the engine to warm up. Little did I know is that he un plugged the power to the battery. (Error #1)
Finished the EFIS work, checked the oil and fuel levels pulled it out of the hangar. Started up and noticed that the battery only read 13.7 v. I have a 12v system, Hmm this seemed low and kelp a mental note thinking my voltage regulator or alternator needs to be checked when I get back but that I could live with it. Took off climbed to 4,000msl and circled Arlington airport to stay within gliding range in case the engine quit.
All engine parameters were normal except my engine oil temp was too high but within limits.
Then 15 mins after takeoff I heard a pop and the engine quit and everything went dead! Nothing worked except my standby static instruments and the EFIS displays which had their own backup batteries. Radios were out to. I instantly got angry! What the heck? Retrimmed the plane and ran the engine out check list in about 10 secs
I wasn’t concerned with making the runway, I was at 4000 ft msl and pretty much perfectly positioned two mile E of the airfield for a right hand turn to final for a landing on RW34. Plenty of altitude to easily glide to the airfield!
In addition I knew that if I switched to my aux battery the engine would begin running again. I was also rerunning the other checklist but nothing improved my situation.
So I thought well I’ve practiced this maneuver before I took the airplane apart so I’ll just descend down to the runway and land, and if I need to start the engine it’s always available.
By the way when I landed in the farmers field I had a nice touch down and rolled out for about five hundred feet. It was at the very end of the roll out when the left main wheel encountered a muddy spot and it came to s stop. This mud instantly pulled the nose to the left but the aircraft’s momentum kept it going in a straight line for about four feet which put a large side load on the right main gear. The right side brace stud broke. That was the only damage.
So as I descended I lined up with the runway, already at my best glide speed with my spinner right at the mid pt of the runway. Than I noticed my spinner moving towards the far end of the runway. Added some flaps and the spinner moved back to the mid pt of the runway.
Then being a perfectionist, I thought I should be able to put this thing down within the 1st thousand ft!
So I went to the second flap detent and the spinner pointed at a spot about a thousand ft from the APPCH end. I’ve got this now I thought!
As I descended further the spinner now began to obscure the first third of the runway and move towards the mid pt again. I decided to live with this condition.
I reviewed the emergency landing gear extension procedure and reminded myself that once it’s extended it won’t retract without electricity.
So I would not extend the gear until I had the runway made.
Passing thru a thousand feet everything looked good but I started to feel the pangs of concern about not having the gear extended. I reminded my self that the gear wasn’t going to be extended until 200’ agl or lower.
Descended on down to 300’ agl and took the flaps back up to 10° and was concerned about the road that crossed short of the approach end of RW34 had some logging trucks going by.
Got down to 200’ agl and began to realize that I could still clear the tops of the trucks and my spinner was obscuring the first half of the runway. Also I knew that the gear would take about 7 to 10 seconds to extend and also pump it down to where it had pressure holding it in position. But flying the plane and pumping the handle it might make it a bit longer. I had no gear lights.
So about 120 to 50 feet I positioned the gear switch down, the emergency extend valve down and lowered the gear. Instantly the nose pitched down and was aimed at the approach lights area. I raised the flaps to extend the glide. This didn’t help
Now I either went around or turned left 45° to land in the farmer’s field.
I was so low that I felt that it was too late to start the engine because if it didn’t start I was still going to land in the farmers field. And I especially didn’t want to land short of the runway and hit a truck or car. So I turned left, did a quick off field landing checklist and I was down.
So why did I land short when I had practiced this same procedure many times before?
Normally I didn’t think this post would really be worthy of a mention to the Glasair owners because most of them don’t change their airplane as I did.
You can prepare as much as possible for any eventuality while flying but this is one consideration that I didn’t believe I needed to prepare for if I had to do an engine out landing. In fact I couldn’t figure out why I landed short as much as I did. It took me three or four days to figure it out and then when I did the math I realized that this is one situation that I had not prepared for.
In a Glasair II if you measure the distance your eyes are positioned above the top of the cowling it’s not very much. What, ten or twelve inches? If you then increase the length of the cowling by six inches, remember I moved my engine forward over 6 inches to make up for the lack of propeller weight, it gives you the optical impression that you are going to land longer down the runway than you actually are. In my case around 800’ farther down the runway! The easy way to prove this for yourself is to take your airplane, and look at the end of your spinner as your on approach at about 500’ agl. This is your usual sight picture the one your used to. Now imagine your spinner is 7 inches longer. Where is your new touchdown point now? Yup it’s farther down the runway.
So the other issues are why did the engine quit? That’s pretty simple. I have no magnetos, I use two electronic ignitions that worked flawlessly as long as they are being supplied with electricity. Then in the event that they are not receiving power I should switch to the auxiliary battery. What I found out about my system was that unlike a lead acid battery the battery management system on my lithium batteries will protect my battery at all cost. Even if it means shutting down power from my main battery.
Remember when I said that I was adjusting my EFIS display and had asked
my tech to turn on the engine heat? Well while sitting in the airplane he Dutifully unplugged the power to the battery and plugged in the heater with the same cord. Oops! (Error#2) So now I am running the EFIS displays on battery power for the next 45 minutes. This is my fault for not checking and making available a separate cord for electrical power to the battery.
Finally, it would of been a nice touch if I hadn’t had the alternator switch turned off! (Error 3) Normally when I get in the airplane I double check that the master switch is on and the alternator switches are on at the same time because they’re right together. This way I can check the hydraulic pressure and the lights. But for some reason that day I didn’t do it or because my feet are so big I could’ve hit it off with the toe of my shoe while climbing in. So that’s why the engine quit after only 15 minutes of running. This was very confusing to me because I still thought I should have had plenty of battery power enough to last for at least another hour. Which caused me to incorrectly diagnose what the problem was with my electric system.
What about the 13.7volts? Unlike a lead acid battery a lithium battery when it is brand new usually indicates about 13.7 V of output. So when I saw it before I took off, I believe that it was working OK and that there was some other problem with my alternator. Now however, anytime the engine is running and I display less than 14.2 v Then there is a problem and that I should shut down and investigate. I will not fly the plane unless I see 14.2v displayed before takeoff. I’ve also added a battery indicating system where I can read the volts available and the percentage of charge. This is part of my checklist items before I takeoff.
Also I have revamped my checklist. There’s no less than three places where I check the position of my alternator switch before takeoff.
And if you’re wondering yes I flew the airplane yesterday and I have flown that airplane over 300 hours since that incident.
So in over 45 years of flying a variety of airplanes from jet’s to gliders and over 25,000 flight hours this is the only time I’ve ever hurt an airplane. This incident cost about $1000 to repair. And I paid for it out of my own pocket so that everybody’s insurance rates wouldn’t go up.
I hope this can help somebody in the future.